Racks and Gears
What is a Rack and Pinion? How Does It Work?
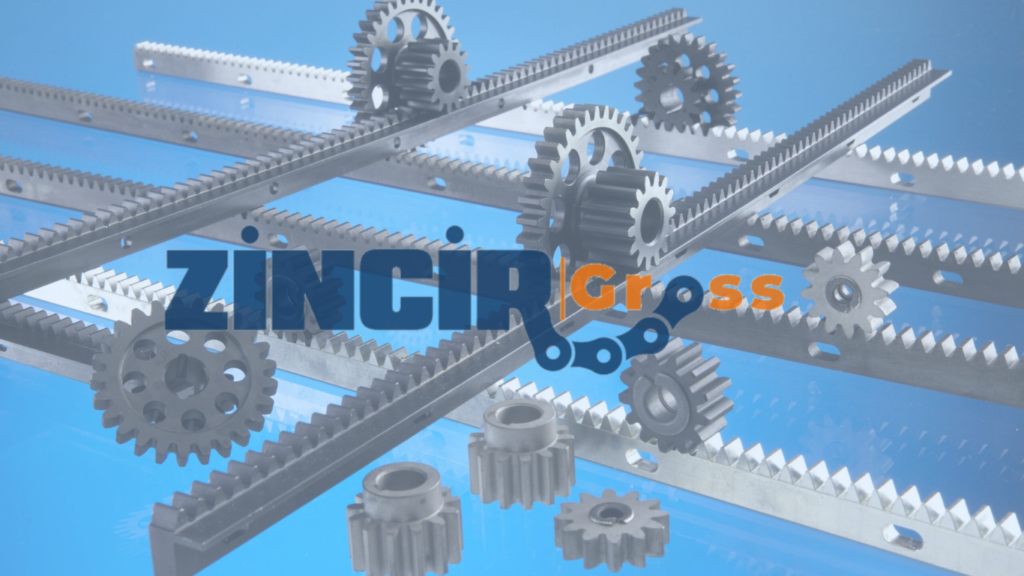
Rack and Pinion Gear Basics
In gear terminology, when two gears come together, the pinion gear is the smaller of the two and typically provides the input in a gear reduction process (in a rack and pinion system, it is the single cylindrical gear). The larger one is simply called the gear (in a rack and pinion system, this is referred to as the rack gear). A rack can be thought of as a gear piece with an infinite radius, or more simply, a straight bar with gear teeth. A rack is a useful tool for making round gears because these straight lines are easy to machine. Once hardened and sharpened, the rack can cut the curved tooth faces into a round block. This process is called gear generating, one of several processes by which gears are made.
Where is the Pinion Gear Used?
Factors to Consider for Pinion Gears
There are three main types of pinion gear sets. Those with straight teeth have teeth that run straight along the length of the rack gear and form a perpendicular angle. Spur or helical gears, as seen in the image above, have angled teeth. Helical gears are more efficient and quieter than straight gears because their teeth engage with the rack more gradually. Due to the increased contact length, helical gears can carry heavier loads. However, in parallel shafts, helical gears create a thrust component against the rack gear and the pinion gear. Thrust can add lateral loads to machine structures.
In roller pinion drives, the rack and pinion gears feature bearing-supported rollers that engage with a specially cut rack instead of standard teeth (resembling the reverse of a bicycle gear and chain, where gears contain rollers instead of chains). These are designed to reduce backlash, sometimes eliminating it entirely.
In general, while rack and pinion systems do not offer as much mechanical power as other systems, they compensate for this with increased feedback. For example, a vehicle equipped with a rack and pinion system in its steering column offers better steering feel.
Rack and Pinion Gear Applications
Several examples of rack and pinion gears are found in industrial and consumer applications such as valves, pneumatic cylinders, machine tools, and automotive systems. Rack and pinion gears make excellent actuators for quarter-turn butterfly and ball valves, which are limited to fixed angles like 90°. In these cases, the rack gear drives the pinion gear to convert linear motion into rotary motion. Rack lengths can be relatively short, offering compact designs capable of providing significant torque.
What are the Types of Pinion Gears?
Similarly, paired with pneumatic cylinders, rack and pinion systems are used to produce limited rotary motion for high-torque motion control operations. They are used in elevators and doors.
Rack and pinion drives are employed in machine tools, pick-and-place mechanisms, and similar applications to provide linear motion. In some cases, lead screws or ball screws may be preferred for shorter movements, but rack and pinion systems offer an economical way to handle longer distances. One disadvantage is that a certain gap is needed for proper meshing between the rack and pinion, which can result in backlash. Depending on the gear size and tooth pitch, recommended backlash can range from less than 0.002 inches to as much as 0.025 inches. For something like a CNC plasma cutter, backlash may not affect the quality of the cut product, but it will definitely be a factor in precision equipment. Rack and pinion gear manufacturers offer zero-backlash designs using technologies like dual or split pinions for these purposes. Additionally, relatively new roller-pinion systems are gaining traction in certain markets.
In the automotive market, rack and pinion steering columns dominate in cars, light trucks, and SUVs (recirculating-ball systems are used for larger vehicles). These systems are variable-ratio steering chains.
Motorcycle chains and forklift chains have different structures.
All Rights Reserved © 2025 – Bilgeweb